A ShapeGrabber expert discusses use and benefits when using OGP’s ShapeGrabber scanners in the medical manufacturing industry.
1. What makes a ShapeGrabber® 3D scanner a good fit for today’s manufacturing measurement requirements?
The ShapeGrabber product line from Optical Gaging Products (OGP®) consists of true metrology class 3D scanners. The accuracy and ease of use of these devices bring 3D scanning out of the R&D labs and into the quality departments. The latest generation ShapeGrabber scanners offer a scanhead tilt axis in addition to the integrated rotary table for maximum part coverage with minimum part handling. Using a scanner to capture a part’s entire surface ensures the whole part is dimensionally correct and nothing is missed.
2. What additional benefits are there when using a 3D scanner, above and beyond traditional measurements?
While traditional measuring devices typically output numerical values, a 3D scanner can output a digital representation of the entire part. This digital copy can be archived and reviewed in the future. An initial inspection may only check a handful of characteristics, but with the digital copy new dimensions can be checked after the physical part has left the quality lab. The ability to compare one part scan directly to another means you can check if the part you manufactured today matches the part you shipped a month ago.
An entire part scan also offers unprecedented visualization capabilities. Comparison of the whole manufactured part to nominal geometry highlights deviations in ways easy to understand by people outside the quality department.
3. Where have ShapeGrabber scanners been successfully implemented within the medical manufacturing industry?
The geometry of manufactured parts only gets more complex. This is especially true of orthopedic implants that need to interface with other functional components as well as human bone and tissue. For years, Depuy Synthes has been making the most of ShapeGrabber scanners for many of their implants. Scanners are also being used to verify tools such as surgical instruments and injection-molded sensor components. In prosthodontics, our scanners are used to verify crowns and abutment positioning.
4. Are 3D scanners easy to use?
Often adopting new technology involves a steep learning curve. That’s not the case with ShapeGrabber scanners. On the data capture side, there are only a handful of parameters to determine the scan envelope and desired level of detail. Defining measurement and reporting requirements uses intuitive 3D software. Once an inspection routine has been established for a given part, running another part really is just a few clicks.
5. How does 3D scanning fit with current trends in medical manufacturing?
Some of the biggest trends include mass customization and even more complex parts fueled by the adoption of additive manufacturing. Customization can create challenges for traditional measurement systems that require a lengthy up front programming step. When the same program is used for many parts of the same part number, the initial programming time becomes much less significant. However, with customization every part can be different and re-programming becomes unwieldy. With a scanner, you capture everything within a fixed volume. If parts fit within the available work envelope the same data capture settings can be reused for a wide variety of parts.
FOR MORE INFO:
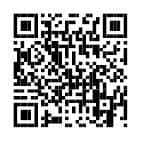