Nearly every manufacturer is now implementing Lean Manufacturing principles. In today’s competitive environment, the drive for continuous improvement is a necessary factor of success for manufacturers in every industry.
Lean processes are intended to eliminate “the expenditure of resources for any goal other than the creation of value for the end customer.” Some goals of Lean include holding little or no inventory, having no idle (or over capacity) machines and maintaining a smooth, logical production flow.
Specifically, 3D laser scanning as part of the quality process can:
- Contribute to improved production flow by introducing significant efficiencies to the quality inspection and measurement processes.
- Reduce both material and manpower waste by providing fast and complete inspection coverage of complex-shaped parts.
The Speed Advantage
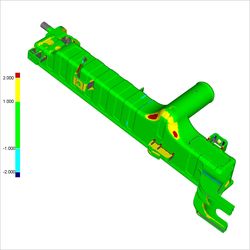
When brought into 3D application software like Geomagic Quality or Polyworks, the 3D scan data supports rapid and accurate quality inspection and measurement.
One of the main advantages of an automated 3D scanner is speed. Traditional inspection techniques – such as manual caliper and micrometer measurements, or touch-probing with a coordinate measuring machine (CMM) or vision system – can take hours (or days) to measure complex parts. Even then, they do not provide enough information to allow for efficient and effective troubleshooting of whole parts, especially complex-shaped parts. These tools can also require specialized skills and resources that may not be readily available.
A ShapeGrabber 3D laser scanner, however, can capture millions of data points in minutes and can be used by almost any trained member of the production staff. Not only is the measurement data collected quickly, but teams are able to make very rapid decisions about how to handle defects due to the amount of data that is captured. Specifically:
- The surface geometry of an entire part can be captured quickly then inspected and measured.
- The 3D scanner outputs a point cloud, which is essentially a complete map of the part’s surface geometry. This can be compared directly to the 3D CAD model to quantify the deviation of the part’s shape from specifications.
- The resulting full-color deviation maps help users to quickly identify the specific part areas that are out of spec. Because the amount of 3D scan data is so great, it is possible to use rich and graphical tools to analyze the data, making troubleshooting intuitive: very subtle defects can be easily seen.
3D scan data of a radiator tank, collected by a ShapeGrabber scanner. Tens to hundreds of thousands of points can be collected in minutes.
Based on this rich 3-dimensional data, quick and informed decisions can be made which dramatically reduce down-time in production as well as reducing defects shipped.
Reduced Waste
Today’s complex-shaped parts – such as injection-molded plastics, metal castings and stampings – include compound curves and multiple features that often stymie traditional measurement tools. By accurately inspecting an entire part and generating a 3D point cloud that represents its complete surface area, errors can be easily spotted which would otherwise be noticed only after production. More thorough inspections during the manufacturing process lead to fewer field defects, fewer returns, and the smooth production flow needed for a lean operation.Automated 3D scanning also helps to reduce other forms of waste:
- Manpower. A ShapeGrabber 3D laser scanner can be easily operated by a technician after about a day of training. There is no need to utilize specialized engineering staff to incorporate the benefits of a ShapeGrabber scanner into the quality inspection process.
- Gauges. An automated 3D scanner can be used to replace multiple traditional hard gauges in the quality inspection process. Doing so enables manufacturers to cut costs and time in a number of areas while increasing production efficiencies.
Proven Technology Supports Current Lean Initiatives
Although industrial 3D scanner technology is robust (at ShapeGrabber we’ve been developing it for 19 years over 5 generations of technology) its use in the quality inspection realm is only recently becoming popular. In today’s highly competitive manufacturing environment, it can be a game-changing tool for companies looking to introduce or improve lean manufacturing processes.