Customer:
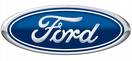
Ford Motor Company
Manufacturing Systems Department
Ford Research Laboratory
Dearborn, Michigan, United States
Background:
The Ford Research Laboratory was developing a new tooling production process using Spray Metal Deposition. This process would reduce production time and offer cost savings over traditional tooling methodologies while maintaining performance characteristics.
Situation:
In developing the Spray Metal Deposition process, the Ford Research Laboratory needed to make 3D measurements of complex tool shapes used at three distinct milestones in the process:
- Completion of the initial tooling model;
- Completion of the ceramic die; and
- Completion of the tool.
Solution:
Using the ShapeGrabber Gantry 3D Scanning System, the Ford Research Laboratory was able to ensure that the initial tooling model, the ceramic die and the final tool were within process specifications. ShapeGrabber’s laser scanner systems scanned components at each milestone and compared the scan data with CAD drawings using Innovmetric’s PolyWorks/InspectorT software (available with ShapeGrabber). Using color maps generated by the ShapeGrabber scans, the Ford Research Laboratory was able to identify areas in which dimensional differences occurred between components and use that information to take corrective action.
“The Ford Research Laboratory is using ShapeGrabber to verify that the Spray Metal Deposition process will provide high quality tooling to a variety of demanding industries in less time, and at less cost, than traditional methods.”
-Joseph A. Szuba
Principal Research Scientist Associate Manufacturing Systems Department Ford Research Laboratory