Customer:
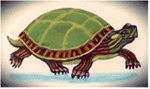
Leafy Green Planet
Massachusetts, USA
Background:
As an award-winning illustrator, Janet Street had long dreamed of including a related toy with her children’s books. To develop toys that met her safety and environmental standards, she started her own company, Leafy Green Planet. Designing and manufacturing renewable, bio-based, and biodegradable children’s toys and kindred products, Leafy Green Planet’s eco-friendly toys are made in the USA.
“Ten years ago, when I designed the first prototype of our Easy Keeper horse toy, my only real option was to have it manufactured in China out of polyurethane, which I did not want to do,” Street recalls. “I didn’t want it to be a polyurethane or petroleum-based product that would just end up in a landfill or the ocean, and I didn’t want to pay the $10,000 minimum order.”
When Street began to hear about 3D printing, she became intrigued. “I really liked the idea that you could use 3D printing to make five or ten prototypes and test a new product,” says Street. “Going from a handmade model to large-scale manufacturing is risky and expensive, and 3D printing looked like it could offer a way around that.”
Before Street could consider printing her prototype, she knew that she needed to find a tool to accurately capture, describe and represent her shape. In researching 3D scanners, Street discovered ShapeGrabber and its automated 3D scanners. Designed to inspect and measure complex shapes, ShapeGrabber’s automated scanners can precisely render every feature of an object with complex curves into a three-dimensional model that can be inspected for defects, further augmented, or reproduced as-is.
Situation:
“Until I found ShapeGrabber, I had no way to create a suitable prototype for production,” Street recalls. “I literally spent two years trying to mold a physical model and create a store-quality toy figure out of green materials. Each time, however, there would be a tiny imperfection and that wasn’t acceptable.”
Fast, Accurate Capture
ShapeGrabber systems capture, describe, and represent complex shapes for use in CAD, CAM, or CAE systems.
“Scanning a toy is not a typical ShapeGrabber project,” explains Pierre Aubrey, President at ShapeGrabber. “We design metrology-class 3D scanners for industrial applications, but when Janet contacted us, we felt that she had a very unique need and we wanted to help.”
While a high-end scanner like the Ai310 wouldn’t normally be required for this kind of application, ShapeGrabber knew that it would generate top-notch results.
“Some of our customers are, in fact, starting to use 3D printing for parts going into aircraft and automobiles,” adds Aubrey.
“ShapeGrabber scanners are ideal tools for measuring these parts for quality control and in the prototyping phase of new product development, and we felt this project would help demonstrate that our equipment can be used for the entire range of manufacturing.”
Using the ShapeGrabber Ai310 scanner, Street was able to see the toy in a new light and obtain the data she needed to 3D print the Easy Keeper model and create a mold from the CAD files. Using non-contact laser scanner technology, the 3D scanner captured millions of data points from the toy and accurately represented the true geometry of the figurine.
“When I saw the results of the scan, it was amazing,” says Street. “It looked fantastic and I could clearly see the slight imperfections that I needed to repair. I’d worked on it for weeks and thought I was done, but the files showed me that there was more to do!”
Unlike traditional methods of 3D measurement that rely on the inspection of a few pre-programmed points, ShapeGrabber’s scanners capture the complete surface area of the part and represent it with a dense “point cloud” of millions of data points. This data can then be manipulated and brought into CAD for editing, archival or analysis, or into CAM software for reproduction. Using specialized 3D scanner software, the point cloud can also be compared directly to the prototype’s existing 3D CAD model in order to optimize the design and manufacturing process and prepare the part for 3D printing.
Solution:
By using an automated, non-contact ShapeGrabber scanner, Leafy Green Planet was able to quickly generate a model that it could use for 3D printing. In addition to speeding inspection – a scan takes only a matter of minutes – the scanner users did not need to write a computer program before scanning the toy.
With an improved prototype in hand thanks to ShapeGrabber, Street is now working on designing a 3D printed metal mold using the ShapeGrabber model. Then, with the help of a local injection molder, her toys will be produced using PLA, a bioplastic made from corn.
“Our goal is to be certified as a producer of safe, eco-friendly products for young children and thanks to ShapeGrabber, we’ve been able to move forward with our dream and start turning it into reality,” Street concludes.
About Leafy Green Planet
Leafy Green Planet. Renew your world. We design and make children’s toys from non-toxic, eco-friendly materials.
“When I saw the results of the scan, it was amazing. My part looked fantastic and I could clearly see the slight imperfections that I needed to repair. I’d worked on it for weeks and thought I was done, but the files showed me that there was more to do!”
-Janet Street
Illustrator, Leafy Green Planet