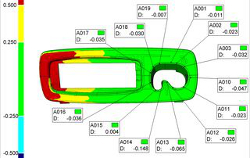
The reason is that traditional inspection equipment – such as manual caliper and micrometer measurements, or touch-probing with a coordinate measuring machine (CMM) or vision system – do not provide enough information to allow effective troubleshooting. These tools may take too long, require expert resources that aren’t readily available, or simply can’t handle very complex shapes. It may be difficult or impossible to obtain dense enough coverage of the part to inspect and identify tough problems. These methods may provide some answers about why a part is not meeting spec but not the whole picture.
Although industrial 3D scanning technology is robust – at ShapeGrabber we’ve been developing it for 19 years over 5 generations of technology – the use of 3D scanning for quality inspection is relatively new. But today, inspection is quickly becoming the number-one application for 3D scanners.
To inspect complex shapes, a 3D laser scanner offers two main benefits:
- It’s fast. A ShapeGrabber 3D scanner can capture millions of data points in minutes. The surface geometry of an entire part can be captured quickly then inspected, measured, compared and decisions made.
- It handles complex shapes. Curves and multiple features aren’t a problem for industrial 3D laser scanners. They scan complete shapes that would otherwise be too time-consuming, costly or simply impossible to measure.
The 3D scanner outputs a point cloud, which is essentially a complete map of the part’s surface geometry. This can be compared directly to the 3D CAD model to quantify the deviation of the part’s shape from specifications.
The resulting full-color deviation maps have helped countless users to quickly identify the specific part areas that are out of spec – and eliminate their most nagging quality control headaches! Because the amount of 3D scan data is so great, it is possible to use rich and graphical tools to analyze the data, making troubleshooting intuitive: very subtle defects can be easily seen. Sample deviation map comparing actual part (3D scan data) to 3D model 3D scanning is known to effectively troubleshoot tough issues such as warpage, twist, voids, fit, die wear, mold manufacturing deficiencies and more. It improves quality inspection efficiencies by enabling rapid Go/No Go decisions. It increases production yields, reduces production time and defects shipped.